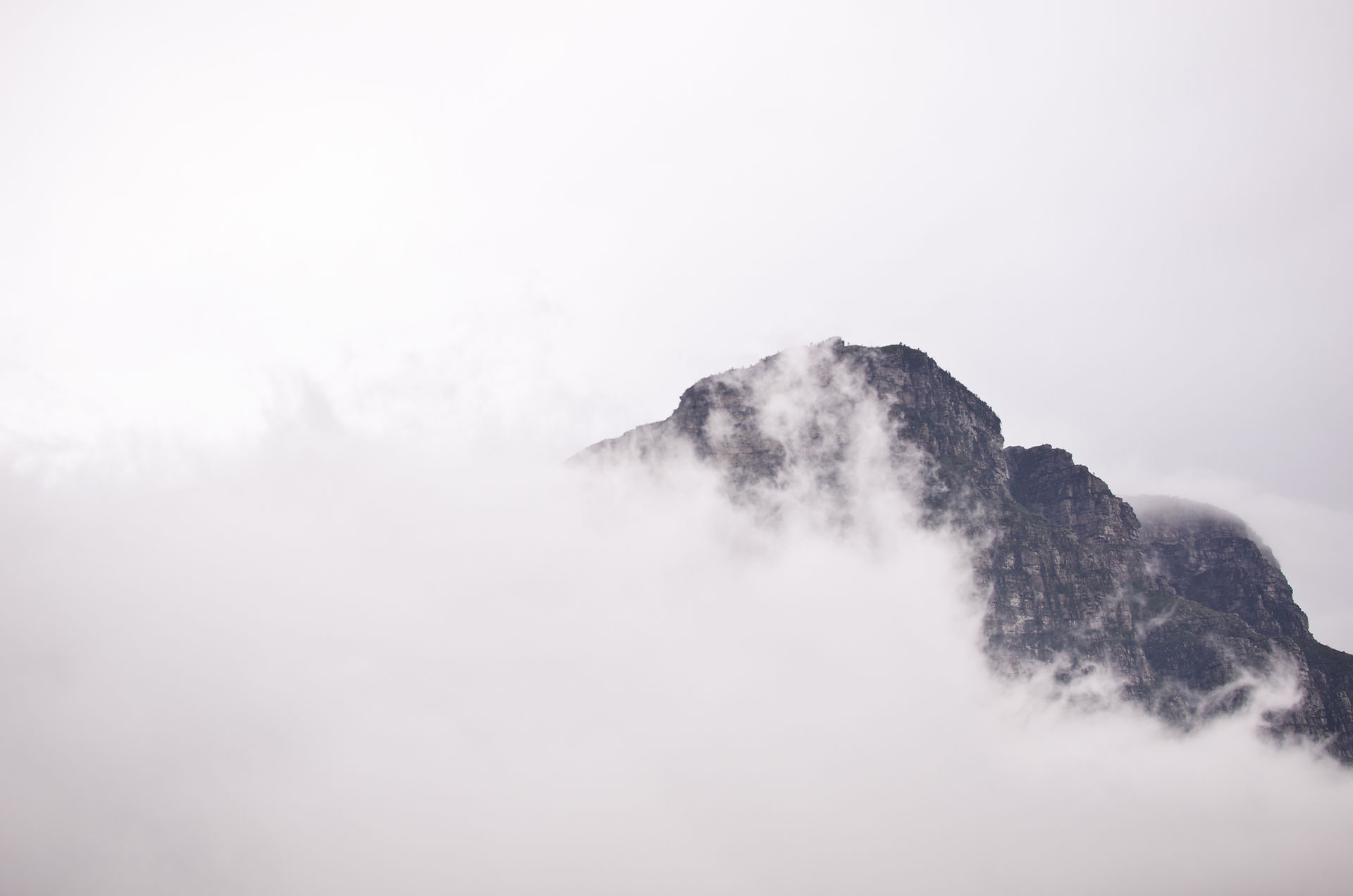
My current research focuses on design, manufacturing, testing and optimization of Heat Sinks, Thermoelectric devices, Solid-state Heat Pumps and overall Air-conditioning system. We also deal with different Surface Coating technologies like Anodization, Sputtering, Polymeric Coating, Electroless and Electroplating. As some parts of these research are still ongoing and some other parts are waiting to be published, I can't share those in details right now but hope to do so as soon as they get published. Feel free to check my already finished and published research projects below. You'll find the full list of my publications in the research homepage.
Enhancing cell adhesion and corrosion performance of titanium alloy by
surface and sub-surface engineering using WEDM
Ti-6Al-4V (grade 5 titanium alloy) is a widely used material for biomedical implant and prostheses. The objective of this study is to investigate the effect of surface and sub-surface characteristics (i.e., surface roughness, microstructure, phase transformation, and recast layer) of Ti-6Al-4V alloy on the cell attachment and corrosion performance after machined by Wire Electric Discharge Machining (WEDM) process. The biocompatibility of titanium alloy has been studied based on the cell adhesion and cell proliferation response of mouse osteoblastic cell MC3T3-E1 to the machined surface of different levels of surface roughness and sub-surface microstructural and phase composition. One conventionally machined surface and one tissue culture treated plastic surface were used for comparison with those four WEDM machined surfaces. It was found that cell attachment increased with increasing surface smoothness, and WEDMed Ti-6Al-4V alloy sample exhibited higher cell attachment compared to even smoother conventionally machined samples. It was found that β phase at the sub-surface favored the cell adhesion on the machined surfaces for EDMed samples. The corrosion rate of machined Ti-6Al-4V alloy samples under simulated body fluid decreases with decreasing surface roughness. The findings suggest that WEDM has the capability of producing implant surface that can promote cell adhesion with improved corrosion performance under body fluid, thus, has the capability to manufacture implants with improved biocompatibility.

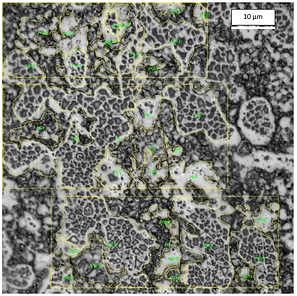
Photos from Surface Topography and Microstructure analysis

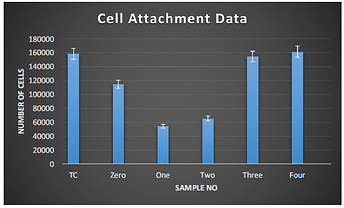
Corrosion test and Cell Attachment test results
A High-Consolidation Electron Beam-Curing Process for Manufacturing Three-Dimensional Advanced Thermoset Composites
This paper describes the application of a new manufacturing process for low-cost and rapid consolidation and curing of advanced thermoset composites that avoids the use of expensive prepreg, autoclaving, and thermally induced curing. The process, called VIPE, uses a novel tooling design that combines vacuum infusion (VI) of a dry preform with resin, a rigidly backed pressure focusing layer (P) made of an elastomer to consolidate the wet preform with uniform pressure, and high-energy electron beam curing (E). A VIPE tool is engineered and fabricated to manufacture 3D laminate bicycle seats composed of woven carbon fiber textile and an electron beam-curable epoxy acrylate. Details of the tooling design discussed include computational fluid dynamics (CFD) simulation of the vacuum infusion, iterative structural finite element analysis (FEA) to synthesize the pressure focusing layer (PFL), structural FEA to design the top mold made of a composite sandwich structure for electron beam transparency, and Monte Carlo electron absorption simulations to specify the e-beam energy level. Ten parts are fabricated using the matched tool (bottom aluminum mold covered with silicone layer and top mold with carbon/epoxy skins separated by foam core) after the dry textile preform contained within is infused with resin, the tool halves are clamped under load, and a 3.0 MeV e-beam machine bombards the tool for less than 1 min. Part thickness, part stiffness, surface roughness, and fiber and void volume fractions measurements show that aerospace quality parts with low cycle times are achievable, although there is high variability due to the small number of replicates and need for process optimization.

Bottom laminate skin, pouring mold for mix-and-pour foam core, and final top mold construction

PFL mask curing using the VIPE top and bottom molds, mask with offset sheet after vulcanization, and final mask
INVESTIGATING THE EFFECT OF WIRE FEED RATE AND WIRE TENSION ON THE CORNER AND PROFILE ACCURACIES DURING WIRE-EDM OF TI-6AL-4V
Ti-6Al-4V (grade 5 titanium alloy) is one of the most widely used materials in aerospace applications including turbine blades for aerospace engines. Due to the difficulty of machining titanium alloys using conventional machining processes, wire-electro-discharge machining (wire-EDM) is used extensively for cutting titanium parts with complex geometries and profiles. The objective of this study is to investigate the effect of two important non-electrical parameters in wire-EDM, i.e. wire feed rate and wire tension, on the geometric corner and profile accuracies of the Ti-6Al-4V parts machined by wire EDM.
A complex profile was designed for machining in two different thicknesses of titanium alloy using each set of experimental parameters. The complex part includes corners with 45, 90 and 112.5, as well as thin wall section for measuring the kerf accuracy. It was found that with the increase of wire tension, the corner accuracies at almost all the angles improved. however, too high wire tension caused inaccuracies by providing larger angles than the target values. The effect of wire tension was dependent on the thickness of the machined part. For thinner workpiece the results of the angles generated barely followed a trend, whereas for thicker part, the measured angles followed an excellent trend. The kerf accuracies were found to improve with the increase of wire tension for thin part, whereas for thick part the results of kerf width accuracies were inconsistent. In case of wire feed rate, it was found that comparatively lower settings of wire feed rates were favorable for machining thinner parts with enhanced corner accuracies. On the other hand, slightly higher wire feed rates provided better corner accuracies for thick part. Besides corner inaccuracy, profile undercuts and deviations from the machining paths were observed for lower wire tensions. Finally, it can be concluded that comparatively lower wire feed rate and higher wire tension provides improved corner and profile accuracies. however, for machining thinner sections using wire-EDM, the trends are not obvious.





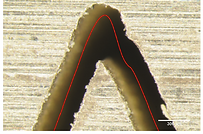
Intended and Actual path of different Wire-EDM cutting angles
Micro-EDM induced surface modification of titanium alloy for biocompatibility
The objective of the current study is to investigate the surface modifications of an implant material Ti-6Al-4V with respect to biocompatibility after machined by micro-electro-discharge machining (micro-EDM). The machined surface characteristics were evaluated by the surface topography, crater sizes, elemental composition, and surface microhardness. It was found that micro-EDM can produce surface roughness lower than 100 microns, which is necessary on the implant surface to promote cell growth around the implant. The roughness of the machined surface can be controlled by controlling the crater sizes, as a direct relationship between crater sizes and discharge energy was observed. A porous and thick titanium oxide (TiO2) layer was observed on the machined surface, which can induce bony ingrowth into the porous structure, resulting in morphological fixation of the implants to the bone. No known toxic substances were observed on the machined surface of Ti-6Al-4V that could be harmful for human body. Moreover, slight increase in microhardness of the machined surface was observed after micro-EDM, which could be beneficial in biomedical orthodontic applications for wear resistance.


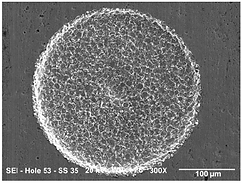
Surface topography comparison of EDM machined Titanium alloys from lower to higher level discharge energy
Published Book Chapters
Chapter 7 - Strategies of improving accuracy in micro-EDM (Micro Electro-Fabrication)
Presently, the application of microelectro-discharge machining (micro-EDM) has been extended to various industries including automotive, biomedical, and semiconductor industries. The accuracy and the process repeatability are two important performance parameters to consider in micro-EDM. Some of the sources of inaccuracy during micro-EDM are stochastic nature of process itself, difficulty in handling very small electrodes, vibration of the tool electrode due to flushing jet, challenges in positioning and changing the electrodes, unpredictable tool wear, and so on. In this chapter, the sources of inaccuracy as well as the solutions to improve the accuracy during various forms of micro-EDM process will be discussed in detail. The current research developments as well as future research focus on the areas of accuracy and repeatability during micro-EDM will also be discussed in the chapter.
Chapter 8 - Hybrid machining and finishing processes (Advanced Machining and Finishing)
This chapter discusses different kinds of hybrid machining and finishing processes that are being developed to meet the continuous upcoming challenges as regards to shape, size, and special application requirements of products. Hybrid machining processes have been broadly classified into assisted, simultaneous, or mixed, and sequential processes of two or more physical processes and/or phenomena. Both conventional (i.e., drilling, milling) and nonconventional (i.e., laser abrasion, electrical discharge machining) machining processes can be combined for hybridization. Various hybrid and sequential machining processes, both conventional and nonconventional, have been discussed with the working principle, specific advantages and disadvantages over a single process, and applications in the manufacturing field. The chapter discusses the requirements and steps that need to be taken into consideration to pull up hybrid machining system and the existing obstacles on the way of doing so. The chapter also recommends future research directions in the areas of hybrid machining and finishing as well as the future significance of hybrid machining in research and industrial fields.
Micromachining of Titanium Alloys (Micro and Nano Machining of Engineering Materials)
Titanium alloys are widely used in aerospace, automotive, and biomedical industries due to their high specific strength (strength-to-weight ratio), excellent mechanical properties, and outstanding corrosion resistance. Although many of the current industrial applications of titanium alloys are at a larger scale, they can be used for microscale applications as well, especially where lightweight, and biocompatibility of titanium alloys are advantageous. Some of the important applications of microstructures made of titanium alloys are next-generation vascular stents, drug-eluting stents (DES), micro-opto-electromechanical systems (MOEMS), microfluidics, and bio-micro-electromechanical systems (bio-MEMS). In this book chapter, a comprehensive overview on micromachining of titanium alloys has been presented. The available literature on conventional, nonconventional, and hybrid micromachining of various titanium alloys has been covered in this book chapter. Starting on the methodology of the process in each case, the book chapter describes the effects of key machining parameters and performance criterions depending on previous works on those respective fields. In addition, micromachining challenges, such as burr formation, tool wear, property change of recast layer, improper surface finish, etc. have been addressed for each machining process and steps to overcome those issues have been suggested. Finally, a reflection on future research directions on the area of micromachining of titanium alloys has been included at the end of the chapter.
Sequential Micro-EDM (Micro-electrical Discharge Machining Processes)
In this chapter, different sequential conventional and non-conventional micromachining processes with micro-EDM have been discussed elaborately with their applications in modern-day research and industrial fields. The necessity and advantages of sequential micromachining processes and their difference from hybrid micromachining have been carefully identified. Micro-EDM combined with micro-grinding, micro-milling, micro-turning, micro-ECM, micro-drilling, laser micromachining , LIGA have been discussed with their advantages over respective single processes. The common issues that generally stand in the way of pulling out sequential processes successfully or hamper their accuracy have also been addressed. The chapter also suggests some initiatives to solve those issues. While wrapping up, the chapter emphasizes on the fact that how sequential micromachining , if properly implied, can solve a lot of problems that currently available single processes are dealing with and widen the vast possibility of micromachining of 3D complex structure with high level of accuracy.